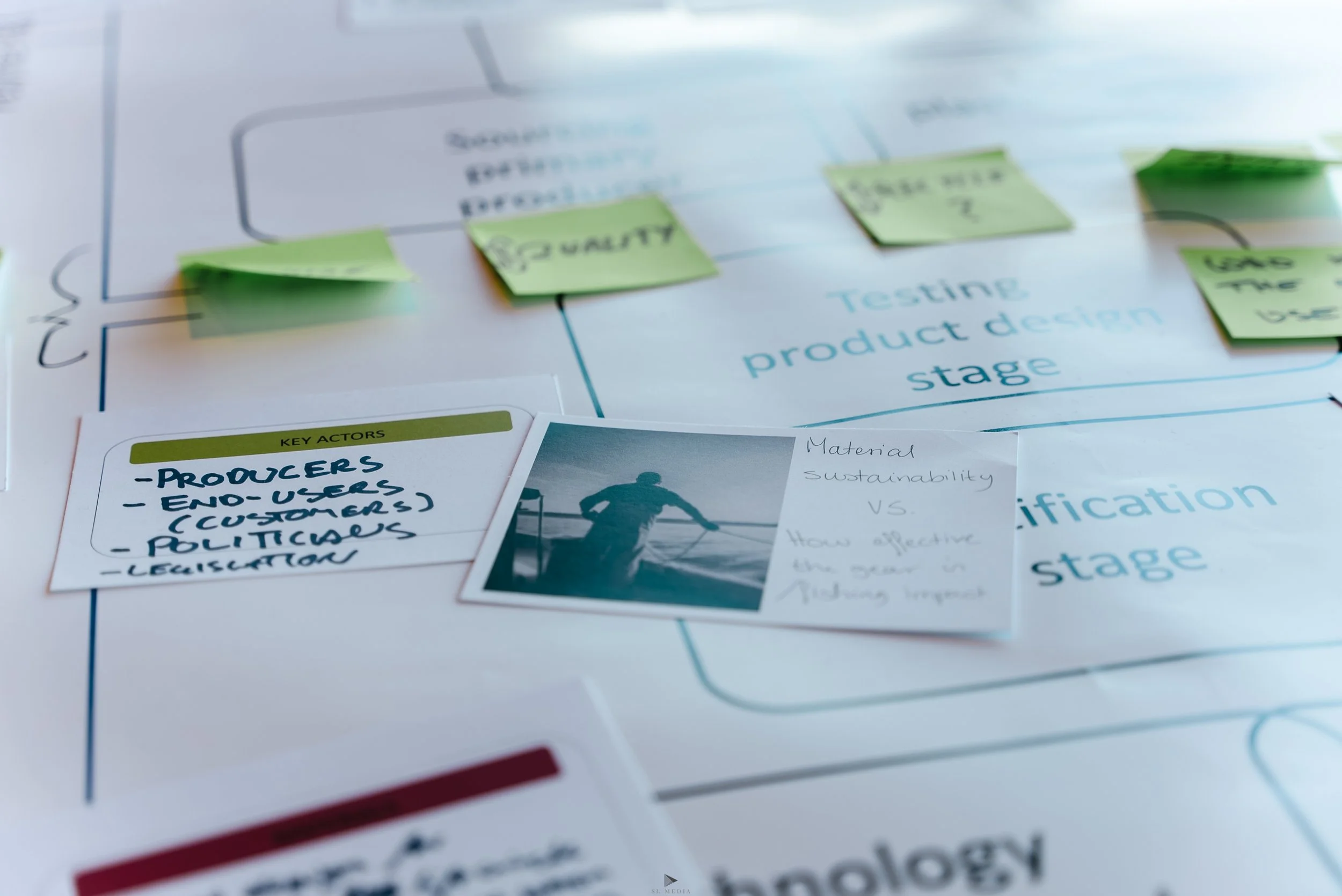
Objective of WP 3 Co-production
T3.1 To establish the current state of plastics use across the value chain service models in the industries of the fisheries and aquaculture sector (stakeholder interviews, short surveys, early workshops).
Using systems and design thinking, the co-production Workshop 1 will seek to:
Build a better understanding of the service model value chain at key intervals to underpin project development work .
Understand specific insights and challenges which present themselves in these industries when adapting for transitions to more Circular Economic Business and Service Models.
What we did: Semi-structured interviews were carried out with purposely selected project partners who represented expertise and knowledge from across the service model value chain. This included several researchers in the areas of material science, material flow analysis (MFA) and life cycle analysis (LCA), public sector policy, industry partners in production, manufacturing, waste management and recycling, reuse and repurpose and end of life activities.[1] The early-stage literature review and interview transcripts were analysed and key points were used to inform the design of the service model workshop and associated tools.
Seven key stages of a service model were established: 1) Research and Development of materials; 2) Production and Manufacturing of gear; 3) In-use stage; 4) Collection at Sea stage; 5) Collection on Land stage; 6) Recycle, reuse, repurpose; and 7) End of Life stage.
Some of these were then combined to create four general stages: 1) Research, product design and manufacturing stages; 2) In Use Stage, 3) Collection Stage and 4) Recycle to End-Of- Life stages.
The tools and methods designed for the workshops were large, table-sized basemaps and information cards (Fig. 1). These were designed and printed for use to promote interaction between participants, discussion of key sections of interest across the value chain, and also to act as an information gathering tool at the workshop.
Who was invited and why: Representatives from all project partners were invited to the workshop, representing all areas of the value chain. Fishermen and aquaculture practitioners will be surveyed separately as it was understood that this was not the best communication tool for them (Stage 1 surveys will be sent to capture their views on the subject).
Group work: Participants were divided into two groups with aligned skills and expertise, e.g., research, product development and manufacturing experts and waste, recycling and end of life experts. Each group was led by a Nordland Research Institute team with expertise in the subject and co-production workshop methods.
The workshop lead presented the general layout of service model value chain sections and emphasised that these were merely key points for discussion based on previous research. The workshop facilitators led the participants step-by-step through each part of the service model value chain, explaining what the tasks were and how to participate. Key areas of interest were: challenges or problems associated with the sustainable use and management of plastics, what practices currently worked well, who were the key decision making actors, what were the key tasks, what types of decisions were being made and why, what were the implications for policy and other relevant key points, etc.
WS Q1. What are the key materials in use? (materials)
WS Q2. Why are these materials used? (decision making)
WS Q3. What are the drivers in making these choices? (drivers)
WS Q4. Who makes these decisions? (key actors)
WS Q5. Impact of these actions? (economic, social, environmental),
WS Q6. Other aspects not considered?
Using the category cards as record-keeping tools, participants were encouraged to discuss their reflections of the service model value chain and the use and management of plastics within this, and record key points from these discussions as the groups were taken through the service model basemaps by the NRI workshop coordinators. Participants were encouraged to be very interactive, and the importance of discussion, debate and recording of decisions was emphasised by the coordinators. The placing of cards and notes could be adjusted across the value chain as discussions concluded with agreed actions and outcomes of plastics use at the key stages of the service model value chain.
Fig. 1 Service Model Value Chain for use of plastics in the fisheries and aquaculture sectors: designed by Megan Palmer-Abbs
Group Activities
Workshop Objective: To establish current practices in the value chain sub sections e.g., research and development, production and manufacturing, in-use, collection, recycle, reuse, repurpose & end of life.
Group work (Groups 1 & 2)
Task 1: Build an understanding of relevant stages of the value chain design & systems thinking tools & methods.
Grp 1: Research and development & production and manufacturing.
Grp 2: Recycle, reuse, repurpose & end of life.
Task 2: Each group will present their findings from the previous task to the other group, and the other group will then give inputs from their perspective on how these value chain subsections currently work.
Grp 1 presents the research and development & production and manufacturing and Grp 2 discusses their views and perspectives.
Grp 2 presents recycle, reuse, repurpose & end of life and Grp 1 discusses their views and perspectives.
Task 3: In use and collection stages: Both groups 1 & 2 will build an understanding of relevant stages of the value chain using design & systems thinking tools & methods.
Task 4: Each group will present their findings from the previous task to the other group, and the other group will then give inputs from their perspective - identify key: materials, decision making/choices, actors, impacts and then what works, what doesn’t work.
The workshop sought to track plastic in the current service models of the fisheries and aquaculture sectors.. However, plastic waste is such an energised topic in the industry that it was inextricable to map current state of FG without including aspirations and existing dialogue of the participants on sustainability and circularity issues (e.g., R&D finance and scope, customer demands on suppliers, RRR business demands on upfront suppliers, public sector demands for better environmental performance and fishermen demands for better waste management systems). The following discussion therefore presents: 1) A summary of the key findings from the value chain mapping which illustrates both current practices, challenges and the drivers which are steering the transition to more circular plastic-based products and suggested associated management practices for improvements of FG for the sectors; 2) a summary of the workshop service model value chain; and 3) Workshop discussion of current state and aspirations for the sectors in terms of circularity.
What we found
The material flow of waste over the life of fishing and aquaculture gear occurs at multiple stages of the value chain of these sectors. This includes but is not limited to plastic-based products which are often complex in their design, structure and related production, maintenance and disposal options. Limiting the environmental impact of plastic-based waste from these products is therefore a complex (wicked) problem. For this reason resolving this issue requires multi actor and organisation cooperation over the whole life of each product. It is pertinent that any solutions acknowledge research and development as an integral part of the issue as well and part of the solution. The establishment of sound science for micro & macro plastics with ‘fit for purpose’ management systems and practices of plastic throughout the life of the product(s), is essential if, the reduction of current environmental impacts as a result of plastic waste from these industries is to be achieved.
Tracking Plastic across the Service Model Chain
The introduction of plastics into the Fishing Gear (FG) service model value chain of the Fisheries and Aquaculture sectors occurred at several stages. The decision-making points for what type of plastic is used, its quality, source(s) and which product(s) it would be used for, were predominantly made at the R&D stage (polymer and product R&D) and at the industry product design and manufacturing stages (ordering of FG). Other points of ingress of plastic-based products into the value chain also occurred during the upkeep (maintenance) of the FG products and then again at the recycle, reuse and repurpose stage of secondary products.
Three main factors critical to the reduction of impacts from the production and use of Fishing and Aquaculture gear are:
1) responsibility is taken at the very start of plastics entering the system (value chain);
2) products are fit for purpose to effectively and efficiently deploy fishing activities (durability & robustness); and,
3) include attributes suitable for circularity (low environmental impact in use, ability to maintain in its primary state for long(er) timeframes, Recycle, Reuse, or Repurpose (RRR), and have the lowest End of Life (EOL) impact.
Key points (interim report)
The following findings are based on the early-stage activities of the SHIFT-PLASTICs project. These recommendations will be reviewed and updated with the user project surveys in late 2022/23. The findings from workshop 1 will inform the approach for workshop 2 and areas for further exploration to develop key principles for more circular service model value chain practices.
Workshop Discussion
At the R&D stage new and existing polymer products enter the value chain as a result of design-based solutions to existing problems. e.g., current performance issues, durability, effectiveness for fishing, social and environmental credentials. Though durability and performance remain strong drivers for change in this area, legislation and policy (global, national and local) now demand a much wider set of credentials (circular design). These policy instruments are, and will continue, to significantly influence the direction of travel for R&D e.g., Circular Economy Directive (EU), Extended Producer Responsibility (EPR).
Existing supply chains and quality: Due to a lack of domestic market and expertise in this area Norway is mainly an importer of plastics. Existing supply chains for plastic polymer materials and/or some Fishing and Aquaculture gear (e.g., certain nets) are generally sourced from Eastern Europe or Asia where overheads are cheaper. The current view of the workshop participants was that the quality and types of plastic polymer sourced for the Norwegian market were more often dictated by the R&D of other nations (e.g., Asian and Eastern European states). The ramifications of this on the environmental performance of these products was therefore subject to external policy and associated quality control and related production and manufacturing behaviours. This was seen as a key issue for Norway in achieving the ambition to produce more circular products for these sectors (e.g., importing low quality polymers or dubious compositions which cannot be readily and effectively recycled). If Norway wishes to improve its environmental credentials for plastics for the fisheries and aquaculture sectors, it will need to overcome these technical and logistical challenges.
New plastic polymer design: The process of introducing or adapting polymers at the R&D stage is time consuming, costly, highly regulated and requires specific test facilities. Testing and standards assurance are critical before a new polymer(s) and associated product(s) can enter the market. It is a fundemental need for the industry to have the capability to assuredly and repeatedly produce materials and products which can withstand the everyday heavy-duty wear and tear (abrasions, friction, degradation, lifetime predictions of materials) of the industry practices and associated environmental impacts (severe weather conditions). In addition, the stability of the polymer within its primary state and when it is used within a composite material is essential (e.g., what is released over time into the sea – e.g., micro plastics, additives, etc). Known as reference materials, these materials need to be tested and proven before they enter the main market. This is a time consuming activity which involves multiple staekholders, activities and communication processes (e.g., R&D processes, regulatory approval, public acceptance, at scale production). In addition, market trust is required to stimulate the entry of new products in to the market. For this reasons, some existing solutions suitable for circular design still lack the kudos and market acceptance to make the market leap. Therefore, support of new innovations which are more circular, need greater support in order that they can enter the market safely but more timeously. It was agreed that incorporating more circular design practices at this stage of the value chain requires a greater focus on a wider set of performance criteria. These should include circular design parameters but in addition require greater fiscal support from policy to drive greater innovation at the market testing and entry stage.
Joint up thinking: New polymers (e.g., biodegradable plastics, new HDPE) appear on the market with regularity. For example, a new type of HDPE has been introduced for feeder pipes in aquaculture that appears to be less brittle, thus limiting fragmented particles into the sea. From a user perspective this is seen as advantageous. However, little appears to be known about the properties and recyclability of this new polymer. In addition, bioplastics hold great potential for some specific parts of FG but currently hold little user support (e.g., use of bioplastics in seine net dolly ropes). There is a need to close the knowledge gap regarding new plastic polymers entering the Norwegian market and provide greater LCA data to enable a comprehensive understanding of the circularity credentials of these products.
Once a suitable plastic polymer is identified various uses will be found at the R&D product and design staged depending upon the qualities of each material. For example, less brittle plastics used in aquaculture plastic feeder pipes, nylon for gillnets. The use of biodegradable plastics is still in its infancy but certain sections of fishing gear more prone to high wear and tear and loss could be niche areas for this new plastic e.g., dolly ropes. The process of introducing new products into the market is time consuming and costly beyond the proof of design and concept. Despite new designs achieving a Technology Readiness (Level (TRL)) and a Minimum Viable Product (MVP), acceptance by the market is fraught with challenges. As with other new industries (e.g., renewable energy) the acceptability of new more circular products will need to navigate and overcome a highly established market system.
[1] This may occur outside of the R&D Stage of the value chain
Product testing and quality control for circularity: In paving the way for such a change, workshop participants saw that an additional stage in the R&D section of the value chain is required. In order to overcome the dysconnectivity between the business sectors involved across the service model, improved collaboration is required on decision making, between and across, the value chain actors. A key additional stage in the value chain should be incorporated which includes product testing and quality control for circularity. This should not be confused with existing quality and testing methods for new products but could be incorporated into this system. Product testing and quality control for circularity should go beyond current polymer and product design paraemters (durability, robustness and toxicity standards). This stage should incorporate more robust communication systems with recycling and end of life actors, accountability and quality control of the polymer and products used, and be set to Norwegian standards for circular design or ‘green design’. From the R&D stage the traceability and inherent quality of plastic-based products should be considered (e.g., draw from blockchain analysis). Whereby secondary use is fully mapped and understood, and the product value and quality are fully understood. This should include a clear overview at the ‘system trajectory level’ and include value retaining processes for each product and sub product(s). This could be a certificated scheme whereby products must be ‘green certified’ to be used in Norway, or similar. Such a scheme should be directly linked to procurement of products entering the Norwegian market. Key performance indicators could be: full cost accountability (including environmental and social impacts), quality, suitable waste collection system, RRR and EOL suitability.
Simplification of material use and design: should also be built in to the system at this early stage of the value chain. Product design(s) should account for the number of polymers used, their quality and suitability for secondary products, simplicity of the product design, the extractable volume of materials suitable for repair, reuse, recycle (including easy disassembly e.g., large sections made from single polymers) and optimal sustainable end-of-life options. Key to success is accurate knowledge about the products themselves e.g., type, quality, additives, functional equivalent and their lifespan (materials and products). To achieve greater circularity in Fishing and Aquaculture gear, this type of information, and the systemic change required to enable more circular choices for the Norwegian market, is required.
Materials and product design: Consideration of the sourcing of the plastic primary producer, primary products and design of product was given collectively due to the close relationship between these activities by producers and manufacturers. Again, accuracy of information and the correct level of dissemination was discussed and seen as critical. Much of the discussion was reflexive of the narrative held at the R&D stage e.g., product substitution with new more circular choices, better regulation and procurement of polymers and products entering Norway that meet Norwegian standards and ambitions (e.g., circular attributes and not just cheapest products and polymer choices). Current market opportunities included replacing parts of existing stock with bioplastics whilst maintaining the performance integrity of the gear e.g., substitution of entrance and buoys in lobster pots or dolly ropes in seine nets with bioplastics. These particular product parts in Fishing gear suffer from both loss at sea, and, due to high abrasive activity are known to release of microplastics. Since they require shorter lifespans than other Fishing gear sections they are seen as perfect for replacement with bioplastics. It is this level of information that all actors involved in the value chain need access so that informed decision can be made.
Further investigation with experts should be sought in workshop 2 for other short, mid and long-term solutions which are ‘fit for purpose’, have a full LCA to determine suitability for circular design and material substitution.
Greater control and ownership of resources within the Norwegian service model value chain could be an option in achieving greater circularity credentials of Fishing and Aquaculture gear. However, Norway has little expertise and established sectors in the ‘cheaper stages’ of the value chain. Some see this as a result of the high wages in Norway and the inevitable outcome that cheaper activities are outsourced to other nations. However, if circularity is applied to these products it is likely that Norway as a primary producer may become more competitive (e.g., LCA or ecological economics baselining the true cost of plastics in FG waste). A reinvigoration of this section of the value chain could be viable for Norway and a means of controlling circularity credentials in these sectors. Focus and investment would need to be considered in areas of logistics, labour force, raw materials, facilities, skills and knowledge and value
In this respect participants welcomed more long-term planning which compared apples and pears, similar to that in LCA methodologies evident in sustainable construction, for the Fisheries and Aquaculture sectors and associate industries.
This should offer sound science and choice mechanisms suitable for the industry to both make the right choices in a balanced way, and illustrate their performance in circular business credentials. e.g., how do you compare and choose between the impact of toxic materials or micro polymer pollution.
Responsibility and Ownership: Once sales and distribution of a product is complete the responsibility of a product through its life journey is vague. Who is responsible for the product from ‘cradle to grave’ and how this is governed remains elusive? As discussed, many suppliers offer maintenance support as a continued service. More attention to this aspect of the value chain could be a ‘quick win’ in elongating the life of products.
Tagging and Tracking: is common mainly in larger scale commercial activities (e.g., barcode or coloured thread in nets, etc)[1]. Norwegian Fishing gear waste monitoring schemes enable the tracking, collection and return of high value waste (e.g., nets) of FG waste. However, discussion from this workshop suggests that instruments or tools are required to educate users on how they can elongate the life of a product. For example, the provision of, and ability to identify suitable responsible collection, RRR and EOL services and to evidence this activity as circular best practice. This includes but is not limited to guidance on maintenance and upkeep of Fishing gear, RRR and EOL options of products, new technology for quality testing beyond just durability & robustness, etc. Of significant importance is mobilising and upskilling the wider circle of responsible actors who sit outwith the production stage with shared vision, incentives and a set of agreed core principles for circularity. This could be knowledge exchange tools, possibly some sort of charter with key actors, which ensures a level of ownership between each relevant party (producers, users, waste collectors, etc). By placing the product central to the discussion and monitoring system (and not the person) improved and more circular systems may be created: ownership should be central to such a system.
Systemic Change: However, to consider this at the production stage of the service model value chain requires systemic change, new business models. Therefore investment in new production lines and simultaneously improvements in collection, waste sorting, RRR and EOL systems (if required) are necessary. This can only be achieved with collaboration and agreement across the various actors (public, private, academic and civil society) involved in Fishing and aquaculture gear. A medium or platform for this discussion is required outside of short-lived projects (over 3 years).
[1] Covered more in depth in next section
Transparency and management off and between all areas of the value chain requires leadership, appropriate management and quality assurance systems if the aspiration of circularity in Fishing and Aquaculture gear is to be realised. Who this responsibility lies with is likely to result in governance innovation in Norway and much more collective, consensual working. This should be led by an independent organisation, suitably experienced to understand the breadth of knowledge, actors and governance issues afoot. The Extended Producers Responsibility (EPR) Scheme will drive this in theory to some extent but in practice much remains to be decided.
Traceability of lost fishing gear: Much discussion was held on labelling practices suitable to secure traceability of lost fishing gear. This is also well represented in the literature as part of the method for waste reduction strategies[9][14]. Solutions such as, electronic tagging, coloured thread in ropes, buoys and related FG design, were discussed. In summary, selecting ‘fit for purpose’ solution which is best practice in reducing the loss of FG should be sought. This should pay due respect to the activity and use of the gear and environment in which it is used. In addition, the historical factors that contribute to this waste should be considered. This includes, but is not limited, to the cost of retrieving the gear against the value of the gear. e.g., cost of fuel to retrieve a lost net. Partners expressed concern that if we ‘jump to soon’ in using electronic tagging, without fully evaluating the parameters of such a decision, we may unwittingly increase the volume and types of waste. This was particularly noted for digital tagging on large FG which is known to lose only fractions of the whole product. In this case it is impossible to tag a whole net and parts of the net will still be lost, possibly with the tag.
Land based Collection: It is generally accepted that Norwegian port collection facilities and services are too few, distanced, and lack the collection storage and sorting required to suitably support the fisheries sector. This part of the system is in real need of leadership, management and synthesis across Norway. Norway has over 4500 ports if we take the definition of a port as a place where you can enter the sea and a coastline of 25,000km [15][17]. No other European country exhibits the challenges evident in Norway in terms of distance and points of entry to the sea [9]
If the new port reception facility (EU Directive) is to be realised then first we must define, map and identify: 1) Define for Norway 'what a port is’ taking in to account national and local geography and accessibility needs; 2) where these ports are; 3) Waste management facility standards and management systems; and, 4) Ensure legislative, fiscal and support mechanisms are in place to provide a ‘fit for purpose collection, waste handling and next step transportation and service system.
Again, waste management systems and standards are required to ensure the service is properly financed, standardised and available in the right place and volumes which reflect fisheries activities. This should take cognisance of both the fisheries and aquaculture sectors, though the latter currently appears to have a more mature operational system.
Port Reception Collection Directive: The introduction of the Port Reception Collection Directive could go some way in driving and supporting this transition and controlling costs incurred by the fishermen for port waste fees. It is anticipated this will enable a standardisation of port collection facilities, though this should not be assumed. Existing actors in collection and waste management are expected to be most visible, however, given the need and nature of the circular economy transition, new ideas and services may come to fruition. ‘Best practice’ guidelines were still recommended that ensure: 1) cleaning of FG; 2) sorting; and, 3) storage were appropriately, effectively and efficiently managed. This was particularly important for those less experienced in this area (including the handling of hazardous waste and biowaste in FG).
Reuse and Repurpose practices: A number of options are available to maintain a product in its primary state, ranging from maintenance to the reuse or repurpose stages. As noted previously, in the main equipment is constantly maintained, repaired and monitored for quality at the in-use stage. If lost gear is retrieved, it is returned to the owner for repair and reuse if they can be identified (e.g., via ID-labelling). This is true for traps, pots and gill nets (70-80%), the top and bottom ropes of the later can be reused.
There are a number of reasons why these kinds of reuse or repurpose activities currently lack momentum in the market: 1) a lack of willingness in key actors; 2) lack of an effective return system; and, 3) old and established behaviour in how to manage waste gear. If information and incentives were available, more could be done to overcome these issues and improve collection and secondary use of Fisheries and aquaculture products. Some quick short term gains could be achieved by users separating and repurposing ropes from nets or the re-manufacturing of mooring systems.
A number of examples of repurposing practices are apparent for fishing nets such as, various types of sport nets, bracelets, dog leashes and handbags (Nofir’s project). Retrieved pots and traps can be donated to schools and children camps (if the owner is not found) for education purposes.
Problematic gear: there are a vast array of products which for several reasons are problematic in terms of recycle, reuse or repurpose. This is due to a number of reasons as follows:
Good quality sorting of recyclate is very important step in the RRR process. Currently there is no requirement for companies depositing ALDFG waste at waste collection points to sort this waste to the standards required for high quality recyclate. Often FG waste is deposited as landfill waste stream to the waste depots. A number of organisations have emerged which do sort waste streams more thoroughly. e.g., IRIS. Once sorted the waste is usually forward to a third party for recycling (e.g., Nofir). However, this section of the value chain is in need of significant investment and overhaul to improve outcomes and realise greater CE practices. For instance, the optimisation of marine debris volumes for recycle, reuse and recondition, development of ‘best practice’ and standardised for the management of ALDFG for the industry. It is advised industries already in this area of expertise could offer high value insights. Ensuring these key areas are in place will enable a smoother transition for record keeping. It is understood the EPR will require the producer(s) to have an accurate record of their products at the RRR and End of Life (EOL) stages. e.g., Nofir a recycling company has a factory in Lithuania where FG and aquaculture gear can be dismantled, different fractions can go to different recyclers.
Looking forward: Due to the established working mechanisms within the value chain of these industry sectors, introducing new ways of working is a challenge. For most organisations in the RRR market, the ability to collect suitable and continuous volumes of Fisheries and Aquaculture waste to run production lines is critical.
Given the vast array of material types and complexity of the gear, achieving this fundamental need in the RRR industry is a challenge. The literature addresses a need to simplify the design and material use in these products and improving collection. However, such is the nature and complexity of the value chain, new ways of working which address the challenge of waste volume creation will require collective solutions (private & public sector) e.g., regulatory and fiscal direction and support.
The true cost of collection schemes, such as voluntary beach collection schemes, whilst valued in terms of their impact on waste in the marine environment and adjacent land (e.g., beaches and salt marsh areas) are not necessarily accounted for in the value chain. This kind of activity should not be devalued but it is very likley this publicly funded activity is not accounted for in the market system. The true cost of this activity should be accounted for under LCA or circular economic calculations. e.g., mass flow economics.
“
“
I want to make sure I have the facts to be circular and be environmentally friendly in a fact-based way and not just a feeling
”
Industry partner, workshop participant (Bodø)
Produced in collaboration with SHIFTPLASTICs project team and partners:
R&D Stages (polymer & product)
The Research and Development Stage (R&D) of the service model value chain of plastic use in the fisheries and aquaculture sectors can be divided into two key stages: the polymer R&D stage and the product R&D stage[1][6][7].
At the polymer R&D stage many decision-making approaches (drivers) determined funding topics and parameters for the sectors. Key influencers were policy actors, environmental agencies, NGOs, membership organisations, etc[6]. Plastic use and impact was one of many competing topics for R&D. For plastic related research the focus can be divided in to two key areas, plastic and non-plastic based materials.
Once funding is secured three key stages occur in the design and testing of new plastic polymers[6], namely, designing, testing and modelling (in situ & under laboratory conditions) of new plastic polymers. This stage is time-consuming and can undergo many calculations and iterations prior to establishing suitable new products.
The product R&D stage may or may not include new plastic polymers and consists of the testing product design stage, and once completed, the certification stage[6]. This is followed by market evaluation, which includes determining the Technology Readiness Level (TRL) of the product, and the expected minimum viable product (MVP])[8]. Once this information is secured, then an established route to market can be sought.[1]
Industry-based product development and manufacturing stages
The product manufacturing stage starts with sales and marketing of products and the processing of customer orders and requirements. The sales and marketing practices generally seek to be reflexive of: 1) customer needs and wants; and, 2) the best products on the market in terms of robustness, durability and cost. The negotiation between these processes is often iterative due to the fact many product(s) scope are made to order e.g., nets for specific fishing boats. In addition, new (improved) products and designs appear on the market with regularity. This is increasing the types and range of materials (including plastic) for the sectors.
Once the product design is agreed, the resourcing of materials is subject to the available resources (e.g., sourcing of plastic primary producer, other primary products). This stage is heavily influenced by the existing and well established industry supply chains and logistics. Primary materials, such as plastic are generally sourced outwith Norway, as a result of cheaper labour forces and manufacturing facilities elsewhere. This is a typical approach for industry wishing to accrue value added. It should be noted that Norways living wage policy specifically adds a different dimension to the scenario compared to other developed nations[7].
The process finalises with the final production and quality assurance of each product followed by the sales and distribution stages. These later stages occur predominantly in Norway.
Workshop Discussion
Ordering scope: This section has some overlaps with the industry-based product and manufacturing stages. At this stage industry have close ties, and communicate well, with their customer base. The customers selection of fishing and aquaculture gear is predominantly affected by personal knowledge and behaviours, and suitability of the gear for the activity in question. These are:
1) the type of fishing stock to be caught;
2) compatibility of the fishing activity with the type of fishing vessel it will be used on; and,
3) the location and type of gear required for aquaculture activities (e.g., coastal or fjord); and
4) Availability and age of the Fishing and Aquaculture stock.
At the product and manufacturing stages design decisions were predominately a result of user preferences (e.g., commercial fishing boat owners, aquaculture organisations). Decisions and scope for the Fishing and Aquaculture gear are based on existing knowledge of the user, the type of activity undertaken, and the design and suitability of the equipment for each boat type or aquaculture farm.
In terms of sales, marketing and customer requirements, performance of Fishing and Aquaculture gear, customer and consumer requirements were seen as key drivers. The design, upkeep and maintenance of the Fishing and Aquaculture gear was seen as pivotal in the choice and selection criteria. As equipment is expensive most purchasers/owners sought products with a long-life expectancy.
Multi-generational behaviour and product selection: A number of factors influenced the ‘lived reality’ which underpinned decision making of the Fishing and Aquaculture gear. Producer and manufacturers had witnessed a change in order requirements over recent months (past 12 months). In response to this changing backdrop, producers stated that they were having to adapt products ‘in real-time’. The industry representatives perspective was that, older generations of fishermen based their equipment choices on more historical facts (e.g., we have, or my family has, always used this material, design, etc). Whilst younger generation fishermen appeared to seek new literature, media insights and customer views about greater environmental credentials of their gear to inform their selection criteria (e.g., sustainability criteria, materials, performance, recyclability, impact, etc). This later point referred specifically to the aquaculture sector where a sustainable, ethical and certifiable product is key for the market. This disparity in decision making was expected to continue as legislation and customer demands moved foward. In addition, the workshop participants felt that some decision making was not as well informed as was first thought.
Whilst alteration in certain gear selection was seen as a ‘positive game changer’, it was generally agreed there was a lack of knowledge and/or green washing in certain areas of these industries. This latter view was a cause of concern and a seen as a distraction in progress to more circular practices. It was agreed that longer term and well-informed decision making for more sustainable and circular products (which took cognisance of sound science, co-working, and step change approaches) was required. In this respect, the right knowledge is required for the wide range of actors who are active across the whole of the value chain. This knowledge must be set and shared at the right level for each actor in a meaningful way (e.g., from complex science-based knowledge to simple consumer base information based on sound science and best practice).
In use Stage
The in-use stage begins with the criteria requirements for each product e.g., fishing nets (seine, gill, etc), aquaculture nets, mooring ropes, pots (lobster, king crabs, etc). Criterion is specific to the type of activity under consideration, the location (deep sea, coastal, etc) and in the case of fishing, the type (size, design, etc) of the vessel. Gear must be robust and durable enough to withstand all manner of impacts over its life span (abrasion from use, environmental impacts, etc) [7][16].
The impact on the gear whilst in-use varies and is dependent uopn multiple factors and practices (e.g., passive fishing (e.g., line fishing) or active fishing (e.g., deep sea trawling)).[9] When not in use Fishing gear may be stored in the sea (e.g., large fishing nets) as this optimises the life of the product. Much of the Aquaculture gear is permently in the sea and undergoes inspection and repair. In terms of fishing gear, this is maintained to some degree by users themselves or a third-party service.[13] There is variability to the quality and diligence of maintenance of Fishing gearboth in terms of routine maintenance and approaches undetaken for repairing snagged or partial breakages in fishing gear[7].
Despite this maintenance activity, marine plastic-based waste is often found in coastal debris highlighting neglectful or careless waste management. This can be whole or parts of gear and is a considerable environmental issue. [10][11][12]. Currently tagging of Fishing gear is evident, (e.g., coloured thread in nets). If found, gear is returned to the fishermen if they can be traced or report missing gear [9]. It is generally accepted most fishermen seek to reuse as much of their gear as is reasonably possible provided its performance is retained. In Norway, nets and gear can currently be returned to suppliers or via collection schemes to key collection points. These are normally at designated harbours.
Workshop Discussion
Transboundary waste and ownership: We have discussed user product selection is influenced by many factors such as type of fish and environment of fishing activity (commercial, recreational, shallow, deep sea, passive or active), cost, availability, personal ideologies and practices of gear selection. In addition participants drew attention to the supplier stage to the in-use section of the value chain. It is common that suppliers often stockpiled supplies (ropes, etc) based on many things but availability is a key component here. For customers there is a sense of irregularity and availability of gear for them which very often has led to them buying ‘what they could get’ at the ‘time it was available’. The aqauculture representatives raised the issue of ‘shelf life’ of products. For example, legislative requirements stipulate that ropes can only be used up to ten years from manufacturing. Therefore, if a rope sits on a suppliers shelf for two years this reduces the active service life of the product to eight years. It is understood that currently supply of gear is a problem due to global recovery from the Covid pandemic. The quality of gear was not discussed much beyond availability and traditional qualities (e.g., durability standards), this part of the value chain should be explored further to identify:
1) What choices of plastic products (polymer and product composition level) are available;
2) Quality control (influencing legislation and polymer) and related information was available; and,
3) How can buyers be enabled to purchase more circular and sustainable products
As discussed, identifying who is actually responsible for marine Fishing and Aquaculture gear is still a major question for the industry. Though it is unknown exactly how the EPR will affect the industries, in preparation for the change, some enterprising work has been undertaken. For example, Lovøld have undertaken a stock monitoring system with Nova Sea to determine the volumes of rope supplies (large and small) they provide. This is respectively divided between mooring systems and nets. The majority (up to 70% is retrievable for recycling but not 100% is suitable for this). The question of ‘how’ to identify responsible owners of gear for a product over its lifetime (which can be up to 15 years) remains uncertain. Due to the complexity and sheer volume of response required for EPR in Norway, the Lovøld stock analysis and other market leader ventures in circular practices, are a good starting point.
Maintenance or upkeep: Fishing gear is expensive and fishermen often try to avoid losing/damaging it. However, there are several factors that can lead to a gear loss, such as bad weather conditions, challenging seabed, and sea ice conditions (applicable for snow crab fishing), and collisions with other gear. Passive fishing gear that are not attached to vessels such as pots, gill nets and long lines are more exposed to these factors.
Particular sections of FG wear faster and are replaced more often than others, for example, the bottom of trawl nets require greater replacement than others and therefore have more established repair and reuse systems. The bigger players in the manufacturing sector have repair facilities alongside their manufacturing factories. (N.B. This does not include gill nets or smaller fishing gear) e.g., Selstad. However, cheaper maintenance options with inferior cleaning credentials could be selected by equipment owners. This was seen as an outcome of misinformed and poor choices by users based on short term cost savings. Cheaper maintenance options for FG often resulted in poor quality washing techniques. This nearly always resulted in poorer results in terms of cleaning, stripping the gear of inherent protective qualities and therefore shortening the lifespan of the gear. Greater attention should be paid to improving access to impartial but accurate maintenance knowledge and the associated longer-term benefits for users. Conversly, the aquaculture sector is highly regulated in terms of product performance, maintenance and waste management. However, it is evident that waste still finds its way into the water (fjords, seas and oceans). There is clear evidence from manufacturers that the aquaculture sector is seeking, and are happy to pay more for, ‘greener products’. The ability to evidence sustainable and green products to customers is increasing. This positive view towards equipment upkeep and monitoring could translate to improved LCA practices e.g., the ability to evidence and report the management of aquaculture products from ‘cradle to grave’.
In practice, the current maintenance of aquaculture gear involves regular checks and maintenance. The use of divers to check nets is common but is usually expensive and not without risk for the divers. The use of robotics is currently being considered, and substitution of professionals from the Oil and Gas industry is apparent in some organisations who are moving to more environmentally friendly practices (e.g., SINTEF have moved some of their activities across in this way to the aquaculture sector). In order to overcome fragments of feeder pipes entering the water system due to brittle qualities of current materials, new more robust HDPE materials have been introduced by some organisations. Discussions to move to more circular cooperative (sharing economy) business models for the supply and management of gear was evident. However, any decisons should consider and work with the recycle, reuse and repurpose actors to ensure the availability of a continuous waste stream for certain plastics with adequate volumes and quality of the waste gear (PE and POE based materials). Without this consideration, the reuse and recycling of by products from the sectors will fall short of minimum viable secondary products (MVSP). This in turn will fail to enable the establishment of new secondary production line(s).
Recreational fishing gear is a known issue due to lighter regulatory obligations on these particular fishermen. Due to the scale of the challenges in unpicking the value chain and plastic use we consider the small-scale recreational fishing to be out of scope for this project. The Norwegian Directorate of Fisheries is currently working on voluntary education packages for this area.
Waste Collection
In Norway collection of fishing gear at sea is well organised and managed through several schemes such as cleaning initiatives by the Norwegian Directorate of Fisheries, the fishing for litter scheme (FFL) and the Fritidsfiskeappen [11][12][13][18] There is a general sense that not enough funding and recognition is available to promote a greater uptake of these kinds of schemes, particularly for smaller actors (commercial and leisure). [11][12][13] For larger companies (fishermen and aquaculture) upholding good waste management systems is more readily upheld due to capacity and ability to do so. For smaller vessels, collection is more problematic due to a lack the onboard capacity to clean, sort and store FG waste whilst at sea. The lack of onshore storage at, and cost of, port deposit arrangements also disincentives the smaller actors to collect FG waste. [7][11][13] A recording system is in place to spot and track waste not collected and GPS mapping allows the coast guard, or similar, to collect waste at sea.[9] However, large quantities of ALDFG remain unaccounted for. [18]
The lack of funding and recognition of the effort it takes to collect FG and deposit it on land is integrally linked with sea collection, and visa-versa. Lack of fit for purpose port reception facilities is a known problem for Norway for two reasons 1) it has a very long coastline, and 2) waste is transboundary and not attributable entirely to Norwegian vessels (circa 30%). [7][11][12][13] Therefore, some improvements in location, capacity and management systems (collection, cleaning, storage and sorting) and then ‘next stage management’ are required. By next stage management we mean repair, recycle, repurpose or End of Life. This is pivotal in improving the circularity of the value chain and associated plastic management.[7][10][11][12][15]
Workshop Discussion
It was acknowledged that marine waste is multi-scalar (local, national, global) and complex in nature. Norway in particular suffers from its long coastline, sparse demography, infrastructure and collection facilities and the ability to collect waste where it naturally collects (ocean currents and FG waste hot spots). The problem of non-Norwegian waste that accrues on the Norwegian coastline and waters was a cause for debate in the workshop, though it should be noted that 70% of waste is attributable to Norwegian activities. That said, despite this technicality, it was agreed that improving domestic waste management and showcasing best practice would support transitions with global counterparts. In turn we suggest lesson can be learnt from other nations and industries who have gone through similar transitions towards circularity [2][16]. e.g., The UK construction waste management scheme WRAP.
Better information is required for users of FG on their products, collection points and services to support the improvement of ‘disposal routes for FG. Collection maturity is required in the service value chain, this requires an appropriate system, that is a collective vision, and involves multiple actors and organisations. Some innovative advances are in action, Nofir collections scheme for example, but this does not address the whole issue under discussion. Currently there is not enough information, the right level of details, and a ‘one stop shop’ for all this information.
Funding and recognition of efforts is a critical issue in encouraging participation in marine waste collection, particular fishermen, but covers a wide range of stakeholders (The Norwegian Directorate of Fisheries, The Norwegian Environment Agency, fishermen, port authorities and waste managers). The Norwegian Directorate of Fisheries has responsibility for annual surveys and FG collection at sea and mapping where collection is most needed. This is 50% funded by the fishermen’s research tax collected at point of fishing sales. The possibility for using insurance companies claims to track ALDFG was raised, in terms of number and type of FG lost, insurance claims, and type of documentation.
Sighting and identifying waste It is well known that ALDFG causes multiple problems for the environment and fishermen themselves (e.g., damage to rudders from trapped FG). In Norway commercial fishermen are required by law to report lost and waste FG. It was acknowledged that smaller boat owners lack the incentive and ability to fully embrace waste collection due to limited on board storage capacity for collection. Currently, recreational fishermen are encouraged to do so via The Norwegian Directorate of Fisheries system (Fritidsfiskappen), reporting is expected to become a legal requirement in 2022. The need and ability to identify and trace owners of lost fishing gear was recognised. The use of various tagging and identification methods was discussed both for the Norwegian market and abroad. Digital tagging, bar codes, fluorescent dyes (natural) were discussed for their suitability and effectiveness. A ‘fit for purpose’ solution which was cost effective and did not run the risk of increasing marine debris was discussed. Concerns were raised that electronic tagging, and the location and number of tags required, depended on the fishing gear, associated wear and tear characteristics and cost (which may be prohibitive). In addition, electronic tagging is not suitable for deep sea fishing due to the limited depths at which sonar technology works or does not work at. Barcode tagging in general was met with a more positive view as multiple tags could be fitted across the FG structure and most vulnerable to breakage and loss material sections. Currently The Norwegian Directorate of Fisheries are trialling electronic tagging to see if this may work in Norway. If the industry could get this ‘right’ then it was felt producers could be held to account more readily for their waste.
In addition, the introduction of the Extended Producers Responsibility (EPR) meant a sense of urgency or need in the industry sectors required some sound, usable solutions for this issue.
Sea Based Collection: and sorting of FG waste on the fishing boats is time consuming and is particular challenging for owners of smaller boats due to their smaller storage capacities. It was agreed that greater guidance and best practice on sea-based collection methods are needed (bags and sorting instructions / guidance, suitable drop of port facilities, more drop of locations, secondary producer avenues, etc). This needed to be simple, applicable and applied across the whole of Norway to ensure appropriate access and services were available for the fishermen and the industry as a whole. This should include an ISO standardisation accreditation and monitoring systems. A system which overcomes the issues for smaller commercial boats would need to be developed to enable this group to participate in waste collection. In Norway ALDFG is predominantly recorded via the GPS on BarentsWatch. The two main collection systems (historical and new waste) in Norway are run by Fishing for Litter (FFL) and The Norwegian Directorate of Fisheries.
Recycle, Reuse or Repurpose
By volume the largest marine litter plastics found in the Norwagian sea and coastal areas is originates from Norway at 70% of total waste [16]. The most problematic being ropes, trawl nets, seines and pots are known to be a particular issue [16]. Norway has a small number of exemplar waste collection and recycling organisations, Nofir, Oceanize, to name a few. However, given the scale of the issue of waste from the industries and regular introduction of new plastic based gear in the supply chain, much more will need to be done to ensure greater circularity. As this is a systemic issue the changes must happen across the whole value chain. This can only be achieved with good communication and decision making, both across, and between, the various actors involved.
Key for those working at the end of the value chain is the quality of the products they receive. This includes 1) the design of the product and ease of dismantling and extracting sub materials; 2) the cleanliness after it has been used and cleaned; 3) the quality of the plastic within the product e.g., plastic polymer (HDPE, PE, etc) and any preservatives or additives (copper or colourings).[7][13][16] In order to achieve the volumes required for a financially sustainable business model good supply chains and collection methods must be established.
This includes sorting and secondary product niche areas (e.g, reuse, re prupose or recycle). An area of rapid innovation is the product processing stage, with existing (repurposing) new methods (chemical and heat methods) are being developed with regularity. This up and coming market is fit for further development. However, not all end products are as sustainable as is sometimes thought[1][7]. To this end, Life Cycle Analysis (LCA) is proving a popular method to identify and substantiate the true costs of secondary products and/or disposal routes.[10][15]
Workshop Discussion
Route of travel for used products: The ability to reuse, recycle or repurpose FG and aquaculture equipment is dependent on a number of factors, namely product quality (strength), robustness and toxicity levels. Sufficient information is required on each product composition to ensure effective decision making on ‘what’ and ‘how’ to manage the RRR stage. This includes information on material composition (polymers and metal parts) and existing waste/recycling opportunities and regulations. For example, cross border regulations of hazardous waste (exported copper impregnated nets). There is also a general lack of industry coordination and/or cooperation which would enable recycling organisations to meet economies of scale for many materials. Often products end up in landfill due to lack of information and viable alternative options rather than a capability to retain secondary value.
Collection as a Service Model: Both NOFIR/Oceanize (Containerservice Ottersøy AS) offer a service to collect Fisheries and aquaculture gear near to source. In the main this is from fishing vessels, net service stations, aquaculture companies, waste-handling companies, and net lofts. Nofir also has a collaborative agreement with the Directorate of Fishermen to collect retrieved FG (gill nets and ropes) from annual clean-up initiative. All waste collected from the aquaculture is registered and traced from fish farmer to service station, through dismantling and to raw material in recycling. Companies use this data to produce sustainability documentation.
Quality Control and Efficiency: The criterion for new products is regulated and therefore sets the standards and decision making around whether a product can be recycled. New products must meet relevant product standards for robustness, durability, and performance. Effectively producing and replicating of recycled plastic-based materials is a challenge for recycling companies due to variability in the quality of plastic polymers in products, the cleanliness of the product received, and the ability to extract reusable material. The outcome of this is that often poor quality recyclate material which can result in 8 out of 10 attempts of chemical recycling failing. This in turn produces additional recyclate waste and greater environmental impacts e.g., additional CO2 emissions and materials waste from processing activities. Standardisation is required which baselines best practices for RRR and Fisheries and aquaculture equipment e.g., ISO standards.
Value for Money: The waste management and RRR stages of these industries are in their infancy. There are three types of recycling techniques for FG: chemical, thermal and mechanical recycling. Chemical recycling has a greater emission (footprint) compared to mechanical recycling. Some limited equipment can be recycled back to the same type of product, and not all equipment is suitable for recycling. Some economically viable niches are apparent with leaders in the market e.g., nylon. Some viable waste products are ropes and PE-tubes; Fishing nets (PA6), when chemically recycled have same quality as virgin material and thus high value. Chemical or mechanical recycling of PA6 that is used in gill nets, purse nets and trawls also has a high value. PP, PE, and mixed PE/PP materials can be mechanically recycled but have a lower value copared to thermal recycled material, but is are still good quality.
However, there are many products with no viable established route to reuse, repurpose or recycle resulting in land fill. Some companies only take Fisheries and aquaculture gear with a high value and low processing need. Therefore low value products are mostly sent to landfill or similar. As landfill is currently cheaper than recycle options product owners have little interest in paying for recycling. It is commonly accepted there is a lack of market incentive to change current practices and behaviour in this respect.
Secondary products: several examples for a production of secondary product were identified. PE/PP can be used for a broad range of new products such as safety equipment for tunnels, shopping baskets, kayaks, garden furniture, different toys, plates, and pipes (PE). PA6 can be used for textiles, carpets, and cloths (e.g., Prada, Burberry, Adidas, Arena),
Some FG waste comprising of HDPE AND LDPE can be used for recycled secondary products such as walkways for the aquaculture companies and trays and chairs for fast food chains (e.g., McDonalds) and mobile phone cases (e.g., Samsung).
Environmental Product Declaration (EPD) Exploring the scope of an EPD could be advantageous for the fisheries and aquaculture sectors across the value chain and beyond. As the Norwegian EPD laws do not cover (at time of writing June 2022) recycled plastics (this also includes Norwegian LCA 140) sit outwith the current system and therefore are not valued as a recycled material. This means that recycled plastic de values a product if recycled materials replace virgin plastics. To further validate RRR schemes in the wider market, some front runners in RRR (e.g., Nofir) are producing an EPD for their product(s). This certification scheme offers suppliers evidence that they are responsibly handling their FG waste materials to their customers. Insights suggest that there is potential to widen the scope of this initiative scope to other materials, such as FG made from recycled polymers, aquaculture gear made from recycled FG HDPE, etc.
End-of-Life
The End-of-Life stage should be considered as an integral part of the secondary product stage. For the purpose of this report we keep this section separate for now. As with the RRR stage, EOL is part of a wider decision-making process based on quality of the product, potential secondary uses and best options for the next stage for the materials. Incineration and landfill are predominantly the choices for this stage. It is generally accepted much waste, plastic based and otherwise, ends up as waste due to inadequate sorting methods or low grade, low quality secondary products.[7][12] Quite often this is a result of the complexity of a product design, poor maintenance, or low-quality collections, cleaning and sorting. Improvements across all these stages could divert much plastic (and other) waste from landfill. This requires suitable methods be built into the value chain system at key stages. [7]
In addition, poor waste management policy (e.g., low landfill tax) allow old, polluting practices to continue. This hides the full cost of waste management and allows material (product and value) to be lost from the value chain. Further investment and (dis)incentives could support a shift in the market to engender greater circular economic practices. This could include the valorisation of waste products and appropriate accounting for waste practices.
Workshop Discussion
This stage is closely connected to the previous RRR one, where the LCA decisions are made to increase the percentage of recyclability for Fishing and Aquaculture equipment. From the sustainability and emission perspectives, it may be more beneficial to recycle the waste. The awareness about this environmental benefit of recycling is increasing in the sector, especially among the younger generation. However, not all waste is suitable for recycling. In order to make sound and fact based decisions for EOL greater attention is required in the total value of a waste product. Current practices include three possible scenarios for: 1) apply suitable recycle methods; 2) send for incineration (can include hear recovery); and, 3) send to landfill (dubious value retention).
Decision making for EOL: There are several factors which affect the decision-making process for the EOL stage of products. This includes guidelines for recycling (developed by Nofir, Container Service and incineration companies), type of waste (mixed materials, the level of its impregnation with copper), the economic cost of recycling, carbon footprint, transport distances to deliver waste, lack of availability of technology for sorting, and in some situations insufficient harbour collection systems. The sectors also suffer from a lack of cohesive regulatory/policy instruments and guidelines for sorting the waste.
Sorting and Processing practices: The sorting process for composite materials in fisheries and aquaculture waste is challenging and is hampered by a lack suitable sorting and disassembly methods. Certain plastics used in the FG usually have a very high quality and precondition for FG recycling (e.g., nylon nets).
However, not all gear is made from homogeneous materials due to the need for quality control and performance in the sector. e.g., certain strength requirements for the equipment in the aquaculture industry can only be achieved by composite materials (e.g., copper impregnated nets). Due to this, some products have more difficult fractions than others, rendering them obsolete for recycling. In addition, there are an increasing number of new products for aquaculture appearing on the market which lack a recycle solution.
In terms of sorting complex design materials, there is a general lack of suitable methods to cut and separate plastic and metal gear from fishing lines. Due to this expense for the waste management facilities, much of the waste may end up at landfill. In addition, not all harbours provide sorting opportunities. As, as a result of this, FG (or parts of it) often ends up in residual waste containers.
This can be avoided if the users of gear (fishermen and aquaculture companies) can contribute to sorting. Moreover, at the incineration stage, there are problems with tangling and the line getting stuck in the incineration system. Therefore, some gear can end up in landfill. Also, when gear is heavily contaminated by marine vegetation it will most probably end up in landfill. This is usually a case for gear collected at the sea by the Directorate of Fisheries during their annual cleaning initiatives. If gear has been in the sea for a long period of time it can be overgrown with marine life and is not suitable for RRR (e.g., recreational fishing gear from shallow waters).
Policy and Legislation: Three main initiatives are proposed to increase the circularity and confine landfill as a last option. First, a set of regulations should stimulate sorting practices by users, i.e., waste sorting before it is delivered to waste collecting/management companies. Second, the initiative should address a need for a better collaboration between the industry and the regulatory actors on new legislations. Third, implementation of the EPR and polluter pay principle (PPP). This final comment, to a certain degree covered in Norway, as with all first-hand sale of fish, a small part of this amount goes into a research tax. Then the generated amount goes to the Institute of Marine Research who works with quotas and to the Directorate of Fisheries to provide the retrieval service. The producer responsibility scheme can help recycling companies, like Nofir, get more material recycled. This would reduce the current situtation were recycle companeis are competing with cheap (and unaccounted for fully in the private sector) landfilling costs.
Ultimately an LCA approach based on scientifically sound decision-making processes should be in place to ensure more circular based decisions are made regarding what, when and why fisheries and aquaculture waste gear enters an EOL facility. This is however, reliant upon an open and transparent system, managed and kept up to date with best science and service availability of the RRR and EOL options for each product. Such a system could be a national electronic decision-making system run and maintained by a independent third-party organisation with the correct expertise to establish and run such a system.
Stage 1 Interim Report
SHIFTPLASTICs NRI Report Team
Megan Palmer-Abbs (WP lead and lead for interviews, workshop, author & media design)
Julia Olsen (interviews, workshop co lead, co-author)
Jens Ørding Hansen (workshop & editing)
Stian Bragtvedt (workshop)
Videographer: Sebastian Loraas - SLoraasMedi